Exactly How Welding Assessment Adds To Durability and Reliability in Fabrication Tasks
Welding examination offers as a foundational element in ensuring the long life and integrity of fabrication projects. By methodically determining potential issues throughout various phases of production, welding inspections not just avoid costly failings but additionally promote a culture of top quality assurance within the group. Employing innovative methods, such as non-destructive screening, assists in thorough assessments while protecting product stability. As tasks progress, the impact of these assessments ends up being increasingly evident, raising crucial concerns about their lasting advantages and implications for total task success. What details techniques can be applied to maximize these advantages?

Relevance of Welding Assessment
Guaranteeing high quality through welding assessment is a crucial part of any type of manufacture task. It works as a protect to confirm that welding processes satisfy well established criteria and specifications, thereby boosting the total honesty of the framework or component being made. Welding examination is not simply a step-by-step step; it is a crucial practice that assists determine prospective issues early, making certain that they are dealt with prior to they rise right into considerable issues.
The relevance of welding assessment can be underscored by its function in keeping safety and security and resilience. Bonded joints are often based on extreme problems, and any kind of issues can jeopardize the efficiency and longevity of the end product. By implementing strenuous assessment methods, organizations can ensure compliance with market laws, therefore decreasing threats related to architectural failings.
Moreover, reliable welding assessment cultivates confidence amongst stakeholders, including customers and regulatory bodies, that the project meets the highest quality criteria. This not only improves the credibility of the producer but additionally adds to long-lasting price savings by avoiding rework and potential obligations. Eventually, welding inspection is indispensable to the success and reliability of construction projects, reinforcing the worth of quality assurance in design practices.
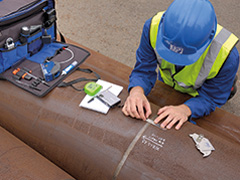
Usual Welding Defects
Welding defects can considerably threaten the architectural honesty of produced parts, making their identification and rectification important. Usual welding flaws can be generally categorized into 3 types: geometric, metallurgical, and service-related.
Geometric problems include concerns such as undercutting, where the base metal is eroded at the edge of the weld, and too much convexity, which can cause tension focus points. These problems can endanger the strength and toughness of the weld joint.
Metallurgical problems occur from improper welding procedures or products, bring about troubles such as porosity, where gas pockets create within the weld, and absence of combination, which takes place when the weld steel fails to bond correctly with the base steel. These problems can substantially damage the weld's efficiency.
Service-related problems may not come to be apparent till after the element remains in use. Instances include fracturing because of thermal tension or fatigue, which can bring about devastating failings if not attended to.
Understanding these typical issues equips makers to implement efficient inspection methods that boost the reliability and long life of their tasks, eventually making certain safety and performance requirements are fulfilled.
Evaluation Strategies and Approaches
A thorough approach to evaluation methods and approaches is essential for minimizing and recognizing welding problems in manufacture tasks. Various techniques are utilized to make sure the stability of welds, consisting of aesthetic examination, ultrasonic screening (UT), radiographic screening (RT), magnetic particle screening (MT), and color penetrant screening (PT) Each strategy has its toughness and specific applications.
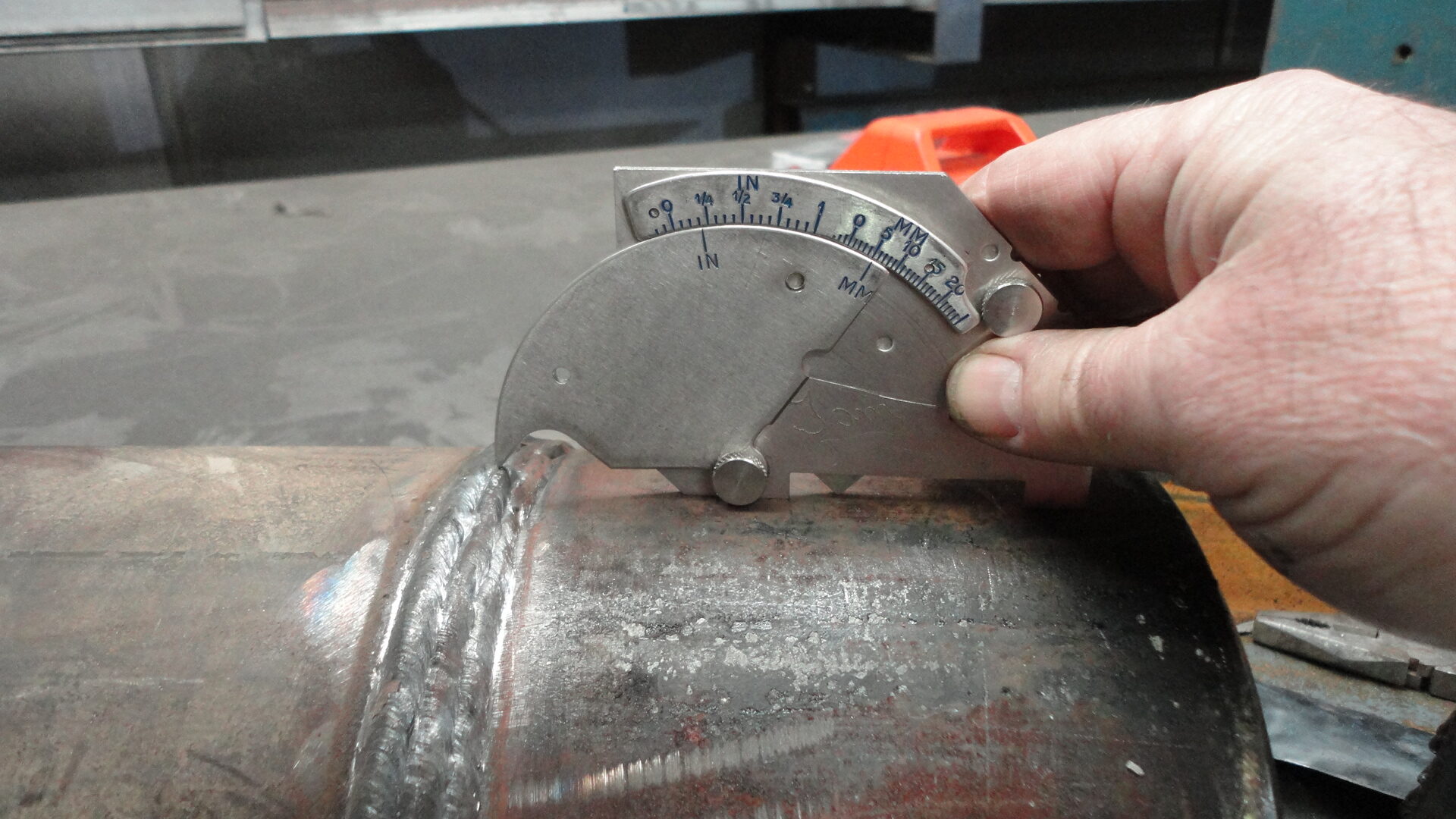
Magnetic bit screening is helpful for discovering surface and near-surface defects in ferromagnetic products. By using an electromagnetic field and using ferrous fragments, inspectors can determine suspensions effectively. Lastly, color penetrant testing highlights surface-breaking flaws you could try this out via the application of a dye that leaks right into fractures, making them visible under ultraviolet light.
Utilizing a mix of these methods makes certain a strenuous evaluation, boosting the dependability of welded frameworks.

Influence On Task Longevity
Reliable evaluation practices considerably affect the durability of fabrication projects. By identifying potential defects and disparities in welding processes, examinations make certain that frameworks are developed to endure functional stress and anxieties gradually. When welds are completely examined, the chance of unnoticed problems, which could bring about structural failures, is lessened.
Routine inspections assist in adherence to industry criteria and policies, which are crucial for making sure the toughness of welded joints. Such conformity not only boosts the integrity of the task however additionally assures stakeholders regarding the high quality of the job. Moreover, prompt detection of imperfections permits rehabilitative actions to be taken early, protecting against costly fixings or complete overhauls down the line.
Additionally, efficient examination practices promote a society of quality assurance within manufacture teams. When employees are mindful that their job will be carefully evaluated, they are more probable to follow best methods and keep high criteria throughout the production process. Inevitably, this dedication to quality not only extends the lifespan of the project however likewise minimizes upkeep expenses, consequently boosting the total financial stability of manufacture undertakings.
Enhancing Dependability in Construction
Reliability in fabrication is dramatically boosted with extensive evaluation processes that resolve possible weaknesses in welding practices. Reliable welding assessment not only identifies issues early however also provides essential responses to welders, making sure adherence to established specs and standards. By making use of non-destructive testing methods, such as radiographic or ultrasonic assessments, fabricators can identify the stability of welds without compromising the product.
Moreover, normal evaluations cultivate a culture of top quality and responsibility among manufacture groups. They are much more most likely to adhere to finest techniques and procedures when welders comprehend that their job is subject to stringent examinations. This proactive technique decreases the risk of expensive failings during the operational stage of a task.
Additionally, complete documentation of evaluation results develops a valuable database of details that can be used for future jobs. Fads in issues can be analyzed to enhance welding methods and training programs (Welding Inspection Milwaukee). Inevitably, enhancing reliability in construction with detailed examination refines not only increases the life expectancy of the produced elements but also strengthens stakeholder confidence in the job's general high quality and longevity. Buying durable welding inspection practices is essential for achieving long-term reliability in any discover this fabrication endeavor.
Verdict
In summary, welding evaluation functions as an essential element in guaranteeing the longevity and integrity of construction projects. By recognizing problems early and employing non-destructive screening techniques, inspections cultivate a culture of quality control that adheres to market standards. The organized documentation of outcomes not only promotes pattern evaluation however also improves accountability and architectural integrity. Eventually, effective welding assessment practices strengthen stakeholder confidence and substantially contribute to the economic stability of fabrication undertakings.
Welding examination serves as a foundational component in making certain the longevity and dependability of manufacture jobs.Ensuring high quality through welding inspection is a critical part of any kind of manufacture project. Inevitably, welding inspection is indispensable to the success and integrity of construction jobs, reinforcing the worth of quality guarantee in design methods.
A thorough approach to evaluation strategies and techniques is necessary for mitigating and recognizing welding defects in fabrication tasks.In recap, welding examination offers as a crucial element in making sure the durability and reliability of fabrication projects.